
How Henkel saves millions of euros per year across its award-winning digital supply chain with Tableau
Data visibility & transparency leads to energy cost savings worth €4 million
20% decrease in energy consumption across Laundry & Home Care supply chain
Using Tableau to monitor global stocks of PPE and operations
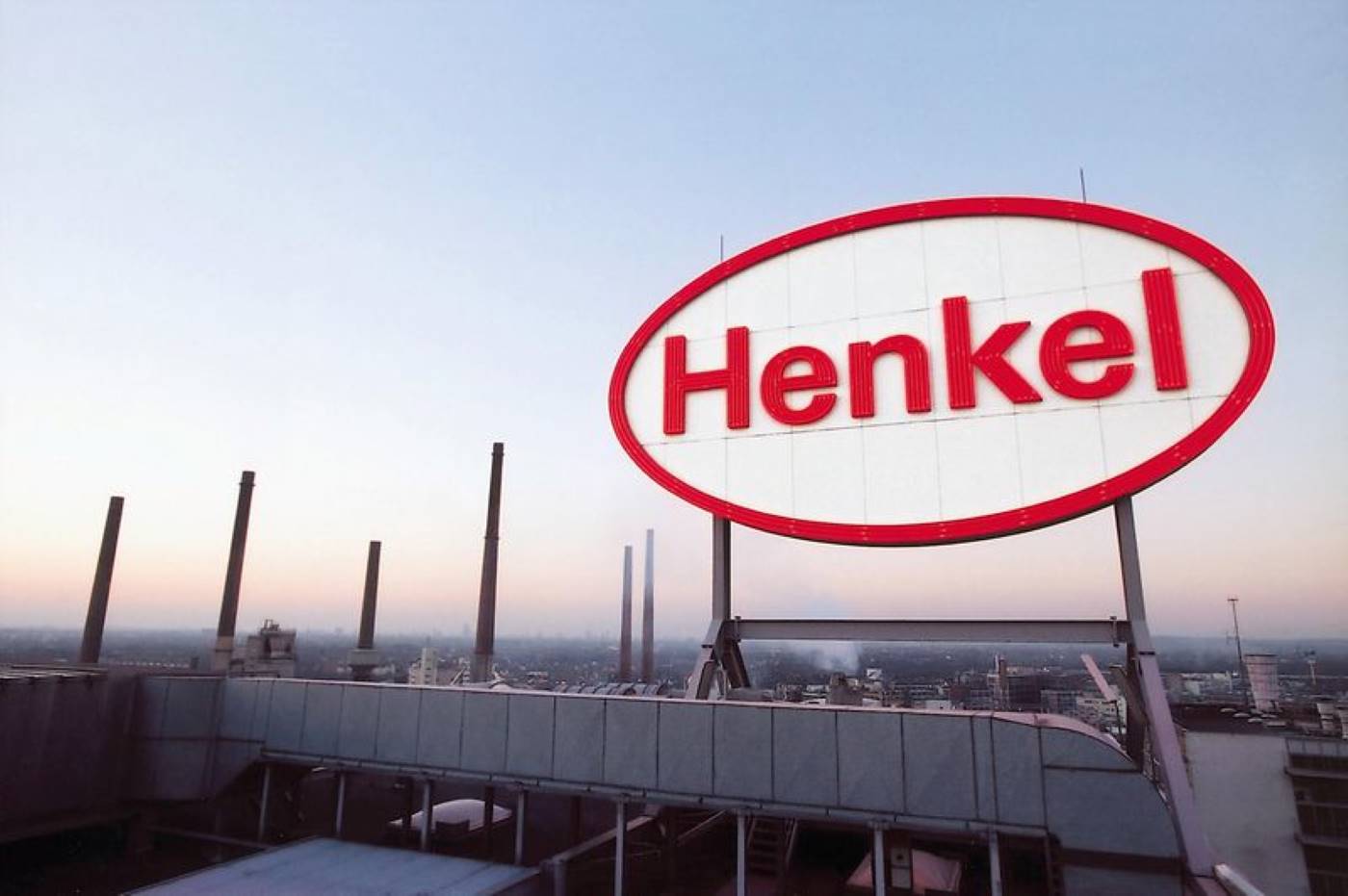
Henkel is one of the world’s leading chemical and consumer goods companies. Headquartered in Düsseldorf, Germany, it employs more than 52,000 staff across its three major divisions: Laundry & Home Care, Adhesives Technologies, and Beauty Care.
Here, Dr Johannes Holtbruegge, Senior Manager Digital Transformation at Henkel Laundry & Home Care, discusses how the company uses Tableau as part of its innovative digital supply chain, to identify millions of euros in operational savings and empower employees with self-serve analytics. In recognition of its industry-leading approach, Henkel was recognized as an Advanced 4th Industrial Revolution Lighthouse by the World Economic Forum (WEF) this year.
What role does data play in Henkel’s operations?
Like so many multinational organisations today, effective data reporting and analytics are critical to Henkel. When operating on such a large scale, even the smallest savings in areas like the supply chain can be worth millions of euros. The more accurate we can be with our data, the more likely we are to identify where such savings can be made.
When did you first implement Tableau at Henkel?
We implemented Tableau in 2016 after a supplier recommended it to us. Before that, we were using simplistic reporting and analytics tools. These were enough for basic tasks, but as our data needs become more sophisticated, they couldn’t provide the advanced functionality we required. Migrating to Tableau marked a turning point for us. We first started connecting our factories worldwide to a central data repository in 2013. Still, it was only after we moved to Tableau that we realised how much of our data we could centralise in one place and the value it could bring in terms of increasing efficiency and identifying cost savings. We now have all of our supply chain data consolidated through Tableau, from a range of sources including Dremio, Oracle, Excel Cubes and more. Doing so has created a single source that everyone in the business can access and use together for the first time.
What kind of savings have you achieved as a result?
In 2019 alone, we identified energy and cost savings worth €4 million, much of which is the direct result of better data visibility and transparency. We’ve also been able to reduce energy consumption across our Laundry & Home Care global supply chain by 20 per cent and improve the efficiency of our factories by over 10 per cent since 2013. Interestingly, all our factories around the world can now see each other’s energy usage and power data in Tableau, which has created healthy competition between them over who can be the most energy-efficient.
Do you have a specific example of Tableau analysis leading to significant savings?
Of course. The production of washing detergent powder is a crucial part of our business. Still, it’s an very energy-intensive process, and the spray towers which turn liquid detergent into powder flakes are highly sensitive to even small fluctuations in temperature and humidity. If conditions are too hot or too humid, their efficiency can be severely affected. However, using Tableau we were able to correlate local weather data against our tower operating schedule, ensuring production was maximised at times where the atmospheric conditions were optimal and vice versa. Doing so has helped to boost production energy efficiency by as much as 5%.
In just six months, our Tableau community has grown from only a handful of central analysts to over 2,100 Henkel users, ranging from global managers to factory line operators.
You recently rolled out self-service analytics to all employees via Tableau. What impact has that had?
Whenever I travel to one of our sites, I see the positive impact that self-service analytics has. Not only can employees now answer many of their own data questions in Tableau, but they can also prepare for meetings faster and share live data with anyone who needs it, in real-time and all at the touch of a button. In just six months, our Tableau community has grown from only a handful of central analysts to over 2,100 Henkel users, ranging from global managers to factory line operators. Many colleagues told me how impressed they are seeing all the things they can do with the data based on Tableau.
Henkel was recently recognized as an Advanced 4th Industrial Revolution Lighthouse by the WEF. What role did Tableau play in this?
The award from the WEF is a great recognition of our work we’ve done to digitize the entire Laundry & Home Care supply chain, and Tableau has been central to that process. The WEF auditors were particularly impressed by our global approach, so much so that they created a whole new Lighthouse category for our initiative - End-to-End Connected Digital Lighthouse - which we took as a big compliment!
Update (May 2020): How is Henkel using Tableau to navigate the ongoing COVID-19 pandemic?
Having Tableau in place, along with the right reports in Tableau Server, means that we've been able to use targeted analytics to maneuver through the COVID-19 crisis as smoothly as possible. All of our major KPIs are online and managers can easily access them from home, which greatly benefits our business steering efforts during this unprecedented time. We also rapidly built a number of important new reports in Tableau to assist with these efforts. This includes a dashboard to monitor our global stocks of personal protective equipment (PPE), ensuring employees are properly protected throughout our facilities. We have also created a sales and operations planning dashboard that managers can access remotely and use to support this critical alignment between disciplines on a local, regional and global level.